OS-SL-T: 1060 Free Shape Optimization Analysis of Bracket
This tutorial demonstrates how to solve a linear static analysis for Bracket model and how to optimize the rib shape of the bracket using Free shape optimization analysis.
- Solve a Linear static analysis for the model
- Solve a Free shape Optimization analysis for the model
- View the results
Launch SimLab
Import the Model
-
From the menu bar, click .
An Import File dialog opens.
- Select the BaseModel.gda file you saved to your working directory from the BaseModel.zip file.
-
Click Open.
The BaseModel.gda file only contains geometric data.The BaseModel.gda file is loaded into the current SimLab database.
Solve Linear Static Analysis
In the following steps, linear static analysis will be defined for the model.
Pressure load will be applied on the face of Sleeve body and Constraints will be applied on the faces of the Bracket body. Tie contact is defined between the sleeve and bracket body. The model setup is solved and the maximum von mises stress value is observed from the analysis.
Define the Solution
-
From the Solutions ribbon,
Physics group, click the
Structrual tool.
The Create Solution dialog opens.
-
From the Create Solution dialog, complete the following
and click OK.
- For name, enter BracketAnalysis.
- For Solver type, select OptiStruct.
- For Solution type, select Linear Static.
- For Select bodies, select all the bodies of the model.
Figure 1. Create Solution
Assign Property to Bodies
In this step, you will assign the Cast Iron property for the Carrier and Cover bodies and the Steel property for the Bolts.
Since SimLab has default materials defined, there is no need to define materials.
-
From the Analysis ribbon,
Property group, click the
Property tool.
The Analysis Property dialog opens.
-
In the modeling window, select the Snap body.
Figure 2. Select Snap Body
-
In the Analysis Property dialog, complete the following
and click Apply.
- For Name, enter Sleeve.
- For Entity, select Solid.
- For Type, select Solid.
- For Behavior, select Isotropic.
- For Material, select Steel.
Figure 3. Property Defined for Sleeve Body
-
In the modeling window, select the Bracket body.
Figure 4. Select Bracket Body
-
In the Analysis Property dialog, complete the following
and click OK.
- For Name, enter Bracket.
- For Entity, select Solid.
- For Type, select Solid.
- For Behavior, select Isotropic.
- For Material, select Steel.
Figure 5. Property Defined for Bracket Body
Pressure Load on Sleeve Face
- From the Analysis ribbon, Loads and Constraints group, click the Loads tool.
-
From the secondary tool set, click the Pressure
tool.
The Pressure dialog opens.
- In the Pressure dialog, enter Pressure for the Name.
- For Pressure, enter 40.
-
In the modeling window, select the Sleeve body.
Figure 6. Select Sleeve Body
-
In the Pressure dialog, click OK.
Figure 7. Pressure Load Input
Fixed Constraint on Bolt Holes
In this step, you will create fixed constraints on the bolt holes of the bracket body.
- From the Analysis ribbon, Loads and Constraints group, click the Contraints tool.
-
From the secondary tool set, click the Fixed tool.
The Fixed Constraint dialog opens.
- In the Fixed Constraint dialog, enter Constraints for the Name.
-
Enable the X, Y, and
Z checkboxes under Displacement.
Figure 8. Create Fixed Constraint
-
In the modeling window, select the bolt hole faces of
the Bracket body.
Figure 9. Select Bolt Holes
- In the Fixed Constraint dialog, click OK.
Symmetry Constraints on Side Faces
Since the Bracket is symmetrical, fixed constraints are defined on the end faces of the model to represent the symmetry.
- From the Analysis ribbon, Loads and Constraints group, click the Contraints tool.
-
From the secondary tool set, click the Fixed tool.
The Fixed Constraint dialog opens.
- In the Fixed Constraint dialog, enter Symmetry_Constraints for the Name.
-
Enable the X checkbox under Displacement.
Figure 10. Create Fixed Constraint
-
In the modeling window, select the side faces of the
model.
Figure 11. Select Side Faces
- In the Fixed Constraint dialog, click OK.
Contact Between Sleeve and Bracket Body
-
From the Analysis ribbon, Loads and
Constraints group, click the Define Auto
Contact satelite tool.
The Define Auto Contact dialog opens.
- In the Define Auto Contact dialog, enter bracket_Sleeve for Name.
-
In the modeling window, select the
Bracket body for Main body.
Figure 12. Main Face Inputs for Contact Creation
-
In the modeling window, select the
Sleeve body for Secondary body.
Figure 13. Secondary Face Inputs for Contact Creation
-
In the Define Contact dialog, define the following
parameters and click OK.
- For Trim, select Secondary and Main.
- For Tolerance, enter 0.1.
- For Face type, select Cylindrical.
- For Contact Type, select TIE.
Figure 14. Define Tie Contact Between Sleeve and Bracket Body
Solve the Solution
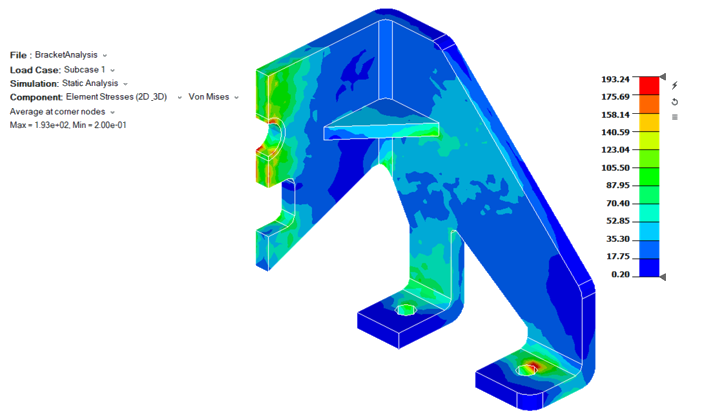
Solve Free Shape Optimization
In the following steps, the shape of the rib will be optimized using the Free shape optimization method to maximize the displacement and constraint the von-mises stress.
Define Optimization
-
From the Solutions ribbon,
Advanced group, click the
Optimization tool.
The Define Optimization dialog opens.
- In the Define Optimization dialog, enter Optimize_Bracket for the Name.
-
Select Free shape for method and click
OK.
Figure 16. Define Free Shape Optimization Solution
Create Design Space
-
From the Analysis ribbon,
Optimization group, click the Design
Space tool.
The FreeShape Design Space dialog opens.
- In the FreeShape Design Space dialog, enter Design_Space for the Name.
-
For Bodies/Faces/Nodes, select the face of the Rib in
the modeling window and click Apply.
Figure 17. Define Design Space for Optimization
Create Design Space Constraints
- In the FreeShape Design Space dialog, click the Constraints tab.
- For Name, enter Design_Space_Constraints.
- For Pattern Constraint, enable the Bilateral Symmetry checkbox.
-
Define the axis for the Pattern Constraint.
-
In the FreeShape Design Space dialog, click
under Grid Constraint.
-
For Face, select the rib face in the modeling window.
Figure 20. Select Rib Face
-
Click Define Vector.
The Define Vector dialog opens.
- In the Define Vector dialog, select Element normal for Direction.
- In the modeling window, select any element of the Rib face and click OK.
-
Create Grid constraint on the supporting face of the bracket.
Create Responses
In this step, you will define displacement and stress response.
You will also define the limit for the stress response.
- From the modeling window, right-click the Optimization solution and select Set Current from the context menu.
-
From the Analysis ribbon,
Optimization group, click the
Response tool.
The Response dialog opens.
-
Define displacement response.
-
Define stress response.
-
Set the limit for the Stress response.
- In the Response dialog, click the Constraint tab.
- For Name, enter Stress_Resp_Constraint.
- For Response, select Stress_Resp.
- Enable the Upper bound checkbox and enter 200.
- Click OK.
Figure 27. Define Constraint for Stress Response
Define Objective
The objective of this optimization is to maximize the displacement.
-
From the Analysis ribbon,
Optimization group, click the
Objective tool.
The Optimization Objective dialog opens.
- In the Optimization Objective dialog, select Maximize for the type.
-
For Response, select Disp_Resp and click
OK.
Figure 28. Define Objective
Solve and View Results
Solve the Solution
Interpret the Results
- In the Animation toolbar, click the Deformation Settings icon and enter 1 for Auto scale.
- For Deformation, select XYZ.
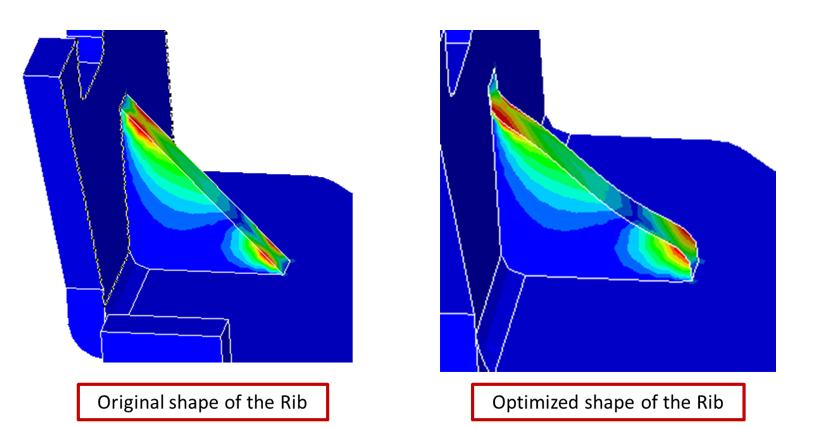