Pulse Steer
A Pulse steer event simulates a vehicle response to a sudden pulse input to the steering wheel while driving in a straight line at a constant speed. The input to the event can be a steering wheel torque or angle, and you can set the pulse magnitude and width. The pulse can be input as a sine, step, or ramp function and you control the width. A drive torque controller is used to maintain a constant speed, and standard outputs for the vehicle and tires are included in the tire System and the output requests system. A plot template is available to plot the results.
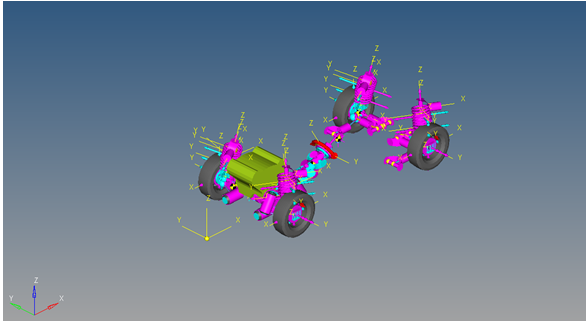
This event is designed to work with a full vehicle model that has been built through the MotionView Assembly Wizard. The event should attach to the model automatically when added through the Task Wizard. It can be used with models built manually, as long as the attachment scheme in the event is strictly followed.
This event is used to determine vehicle response to a sudden pulsed input at the steering wheel. Event parameters are entered on the event form.
Steering Wheel Displacement
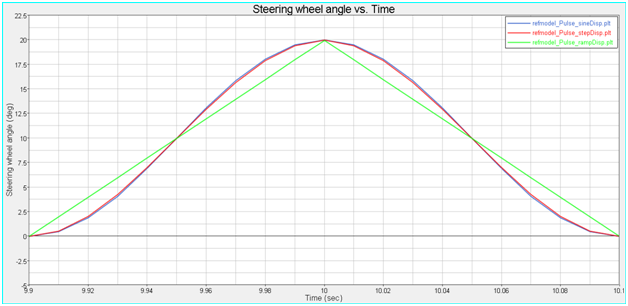
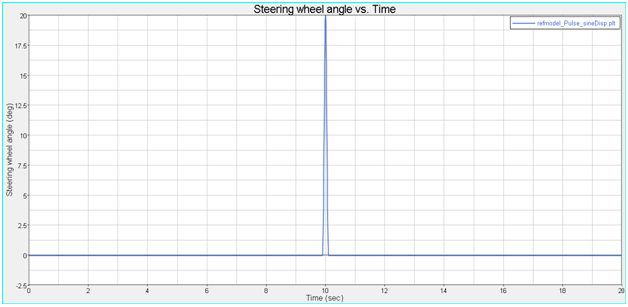
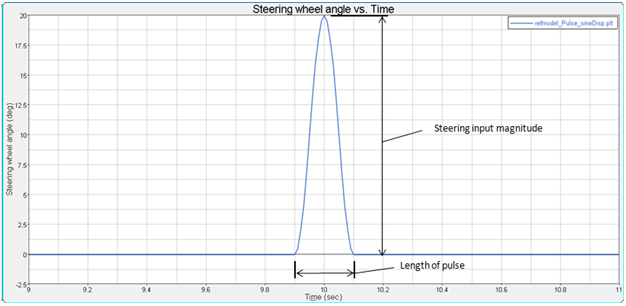
Event Sequence
Time | Description | Purpose |
---|---|---|
0 | Statics | Static analysis with the vehicle fixed to ground and the wheels fixed to the hubs. |
0+ | Joint Release | Two joints holding the vehicle to ground and four joints holding the wheels to the spindle are released. |
0++ | Dynamics | Dynamic event begins with the steering wheel fixed at 0 and the torque controller maintaining constant speed. |
10-1/2 (Length of Pulse) |
Pulse Begins | The pulse event begins, using the method specified in the event form. |
10+1/2 (Length of Pulse) |
Pulse Ends | The pulse event ends, using the method specified in the form. |
20 | Event End | The event terminates. Modify the end time by editing the event template. |
- The steering pulse equations are defined in the event template and refer to the dataset values that are entered using the event form. Advanced users can modify the event by editing the template.
- Our studies indicate that the displacement input method is more stable than force input.
- The event is run on an infinitely flat road surface with no graphics for the road. Add graphics to improve the visualization of the event.
References
ISO +7401-2003 – Road Vehicles-Lateral transient response test methods-Open-loop test methods.
Creating a Pulse Steer Event
- Click the Task Wizard and select the Pulse steer analysis option.
-
Click Finish.
The Model Browser populates with the new data, and the Car/Small truck - Full vehicle tasks dialog opens.
- The Vehicle velocity field determines the velocity the vehicle maintains during the event. Enter a value.
- Enter the steering input type by making a selection in the drop down menu. Angle applies a step angle into the steering wheel; torque applies a step torque into the steering wheel.
- The steering input magnitude determines the magnitude of the steering input that is applied, in either degrees or Newton-mm. A positive value results in a left turn and a negative value turns the vehicle right.
- Enter the length of the pulse, in seconds.
- Select the function type used in the pulse portion of the event.
- Click Next.
-
Click Finish.
The event is created and is displayed in the Model Browser.
-
In the Model Browser, expand Data
Sets and click on Full Vehicle
Data.
The data set information displays in the panel. One dataset is used in the system and it contains the data used to describe the Pulse steer event. The event allows you to set the lateral acceleration, circle radius, steer release time and turn direction (left or right). The initial vehicle velocity, wheel rotational velocities, and ground height are calculated values and should not be changed manually.
-
In the Model Browser, expand Forces
and click on Steering Torque.
The Force panel is displayed. The force in this model is applied to the steering wheel. If the steering wheel and column are not included, the force will be applied to the steering gear input shaft.
-
Click on the Rot Properties tab.
The force is initially defined as zero. The force is redefined in the event template using input from the event form.
-
In the Model Browser, expand Forms
and click on Pulse Steer Data.
The form is the only place that you should change the lane change event. Lateral acceleration, circle radius, turn direction and steer release time are the parameters that can be changed. The ground Z coordinate is a calculated value and is calculated using the wheel CG Z location and the tire rolling radius from the tire data form.
-
In the Model Browser, expand Joints
and click on Rack Dummy Ball Joint.
A ball joint is included in the Pulse steer event. The joint attaches a dummy body to the steering rack. The joint is included to make certain events work in ADAMS.
- If building a model manually, attach the dummy body to the steering rack using the panel.
-
In the Model Browser, expand
Motions.
Three motions are included in the event. The steering motion to the vehicle is provided by the steering controller and acts on a revolute joint that connects the steering column to the vehicle body. If a steering column is not included in the model, the joint acts between the steering rack input shaft and the vehicle body.
The front and rear wheel motions act on the wheel spindle revolute joints that connect the wheel hub to the knuckle. The motion is initially zero (fixing the wheels to the knuckle) so the model converges statically. The motions are deactivated after the static equilibrium analysis to allow the tires to rotate during the dynamic analysis.
-
Click on Steering Wheel Motion.
The panel changes to reflect the new data.
- Make changes as necessary.
-
In the Model Browser, expand
Templates and click on Pulse
steer.
The template is solver specific and only the MotionSolve template is documented. The template is inserted in the solver deck after the </Model> command and controls the execution of the event.The template for this event is shown below. The template has commands for the output files that are generated, the sequence of events that are run, and the run time commands for the forces, joints and motions used to create the pulse steer event sequence.
<ResOutput angle_type = "YPR" /> <ResOutput mrf_file = "TRUE" /> <ResOutput plt_file = "TRUE" /> <H3DOutput switch_on = "TRUE" increment = "1" /> <ResOutput abf_file = "TRUE" /> <!--Initial static analysis --> <Simulate analysis_type = "Static" end_time = "0.0" /> <Deactivate element_type = "MOTION" element_id = "118002" /> <Deactivate element_type = "MOTION" element_id = "218002" /> <Deactivate element_type = "MOTION" element_id = "118003" /> <Deactivate element_type = "MOTION" element_id = "218003" /> <Deactivate element_type = "JPRIM" element_id = "303001" /> <Deactivate element_type = "JPRIM" element_id = "303002" /> <Deactivate element_type = "FORCE" element_id = "31801" /> <Motion_Joint id = "318001" expr = "IF(TIME-9.9:0,0,IF(TIME-10.1:-10D-(-10D) *COS(2*PI*5*(TIME-9.9)),0,0))" /> <Simulate analysis_type = "Transient" end_time = "20" num_steps = "2000" /> <Stop/>